Kenya Airways Boosts UK Maintenance Plans Ahead Of Gatwick Service
LONDON— As Kenya Airways prepares to launch new thrice-weekly service between Nairobi and London Gatwick Airport in July, it is finalizing maintenance plans to support operations.
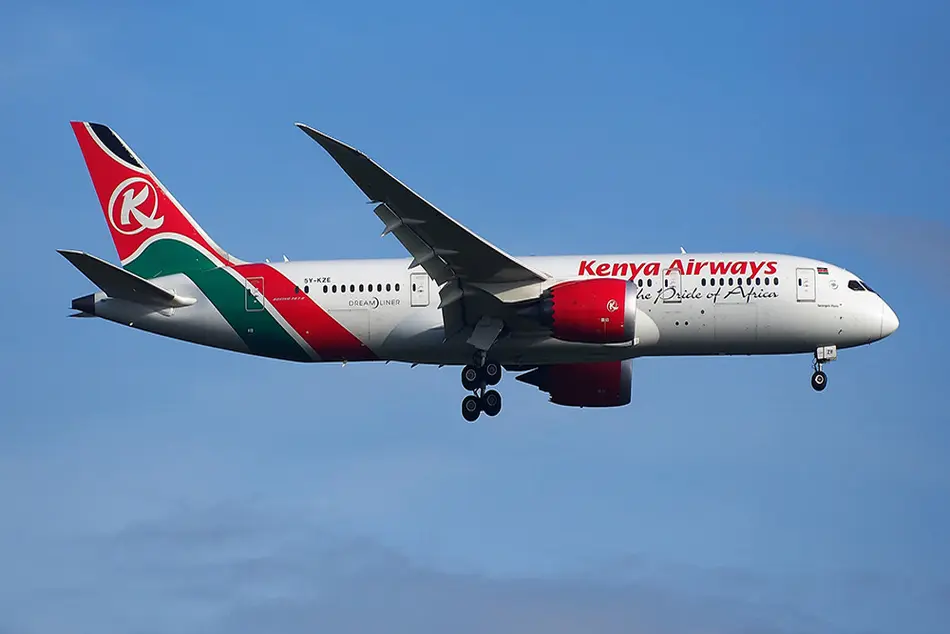
LONDON— As Kenya Airways prepares to launch new thrice-weekly service between Nairobi and London Gatwick Airport in July, it is finalizing maintenance plans to support operations.
While Kenya Airways already serves the London market with daily operations to London Heathrow, it must demonstrate that it has the technical resources and infrastructure in place to support safe and reliable operations on the new route.
To support a smooth entry into service, Kenya Airways is addressing key technical support requirements and line maintenance planning. A critical enabler in this process has been Kenya Airways’ new European Union Aviation Safety Agency Part 145 certification, says Vijay Singh, capability development and MRO sales lead for the airline’s technical department.
“This certification not only enhances our brand but has also been instrumental in facilitating collaboration with the UK Civil Aviation Authority,” Singh tells Aviation Week Network.
“As we prepare to launch the Gatwick service, our flight operations engineering team has carried out comprehensive performance assessments, taking into account fuel capacity, payload optimization, runway performance and seasonal weather patterns along the route,” says Singh.
He further emphasizes that Kenya Airways’ Boeing 787-8 fleet—maintained by the airline’s own MRO division—was thoroughly evaluated for extended-range twin-engine operations performance capability, range performance and compatibility with Gatwick’s operational infrastructure.
Kenya Airways is in the final stages of appointing a certified line maintenance provider at London Gatwick. Singh says the evaluation process has focused on alignment with the airline’s technical standards, responsiveness and the ability to integrate with Kenya Airways’ maintenance control center in Nairobi.
Kenya Airways has also considered securing agreements with third-party maintenance providers or OEMs to ensure spare parts availability. The airline is selectively implementing power-by-the-hour arrangements to enhance cost predictability and ensure timely access to serviceable components. While Singh disclosed no specific contractual details, he emphasizes that the airline maintains strong working relationships with several OEMs and global suppliers.
“We will leverage our internal logistics network and established vendor support system to ensure spare parts can be mobilized quickly whenever the need arises,” he says. “Our supply chain and engineering teams are experienced in executing time-critical spares movements across our network.”
Kenya Airways does not anticipate outsourcing scheduled services such as A checks in the UK since it has its own internal capabilities. However, it has established contingency arrangements with UK-based providers for unplanned support if required.
Some reports have indicated ongoing technical challenges within the Kenya Airways 787 fleet, potentially linked to spare parts availability or broader supply chain constraints. In response, Singh notes that the airline has implemented proactive spare parts planning, predictive maintenance programs and close coordination with OEMs to effectively manage and mitigate such challenges.
“For the Gatwick route, we have put in place additional spares support and contingency planning, and we are confident that there will be no disruption to operations,” he says.
Looking further ahead, Singh highlights the airline’s strategic intent to build long-term resilience. “Our focus is on developing in-house component repair capabilities at our Nairobi facility,” he explains, adding that skilled engineering staff and targeted investments in tooling and infrastructure should position Kenya Airways well to strengthen regional self-reliance and reduce turnaround times through locally executed repair solutions.