CFM RISE Turbine To Face Early Dust Ingestion Testsa
With time on wing a key consideration for its next-generation engine, CFM International has revealed plans to conduct dust ingestion tests of the new high-pressure (HP) turbine blade at the core of its RISE (Revolutionary Innovation for Sustainable Engines) technology initiative.
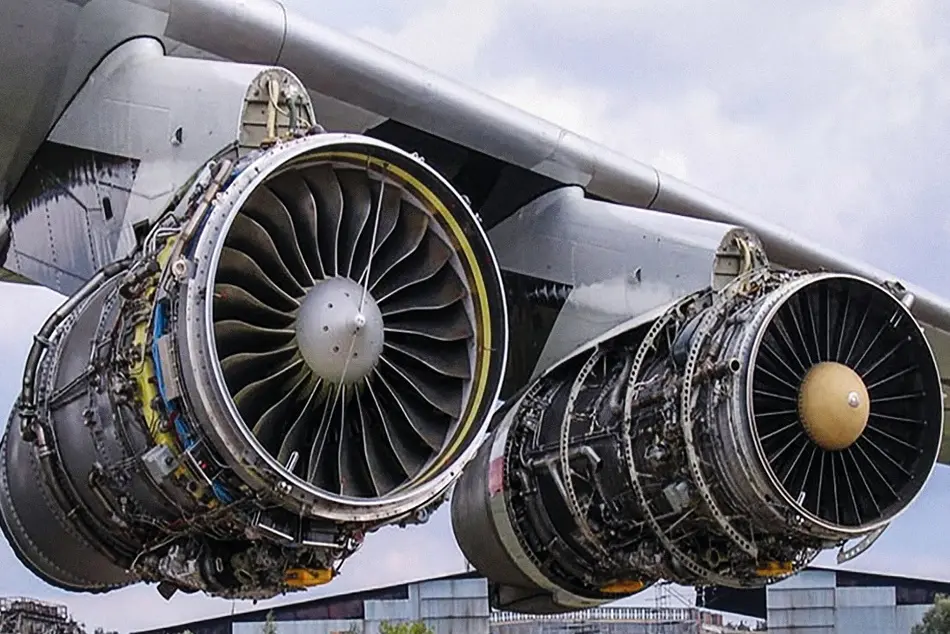
With time on wing a key consideration for its next-generation engine, CFM International has revealed plans to conduct dust ingestion tests of the new high-pressure (HP) turbine blade at the core of its RISE (Revolutionary Innovation for Sustainable Engines) technology initiative.
“We are actually running a durability engine right now,” says Mohamed Ali, vice president and general manager of engineering for GE Aerospace. “So that new design of high-pressure turbine is actually on test for endurance testing, and next year we’ll be testing that same technology with dust.”
Updating progress on RISE at the International Society for Air Breathing Engines (ISABE) in Toulouse, Ali says the additional focus on dust ingestion is “the earliest we’ve ever done that,” and reflects the turbine durability lessons learned from the Leap-1 and other recent GE engines that operate at higher temperatures in challenging environments. The RISE’s compact core design will add to these challenges.
“We had another test to measure performance last year and it really worked as intended. In fact, in some cases, better than we thought it would be,” Ali says.
The dust tests, also known as CMAS (calcium-magnesium-alumino-silicate) tests, evaluate the interaction of molten particles with the thermal barrier coatings (TBC) that protect the turbine blades. TBCs are key to enabling the engine to operate at temperatures up to 1,200C, and CMAS issues can degrade coating performance leading to blade erosion and–in worst cases–component failure.
“We have incredible testing capability for dust, but it’s not as easy as most people think it is. We have spent more than a decade developing that capability. It’s in the dust formula; how we inject the dust, and how we run the test. And trust me, we made quite a few mistakes while gaining this knowledge,” he says.
Recent dust ingestion work on the Leap-1, for example, has been conducted on a specially developed rig in Evendale, Ohio, using bespoke material to replicate the pollutants and dust found in some areas of the world. After much trial and error, the company says it is now able to reproduce the premature wear, tear and failure modes found on the baseline Leap-1 first stage HP turbine blades. “We were able to turn on and turn off that failure mode. So, we feel very confident about that,” Ali says.
Due to the smaller size of the RISE core components, the HP turbine blades and nozzles are being evaluated in an F110 military donor engine. GE says the endurance and follow-on dust tests also “are done in an F110 engine in a test cell. Dust tests will use the dust ingestion test rig we developed, placed in front of the F110 engine.”
As GE focuses largely on the thermodynamic aspects of RISE, CFM joint venture partner Safran continues to evaluate many of the program’s propulsive efficiency advances. Also speaking at ISABE, Pierre Cottenceau, Safran Aircraft Engines vice president, Engineering, Research & Technology, says “there are lots of challenges. Certainly, the open fan has huge potential in terms of fuel reduction, but this will only be achieved if it is properly integrated with the aircraft, and in a lot of different aspects–such as aerodynamics for sure, because there will be some key interactions with the wing.”
So far Safran appears happy with aerodynamic and acoustic results, many of which are from recent static and dynamic tests of a 1.5:1 scale open fan blade set conducted at Onera’s S1MA transonic wind tunnel in Modane Avrieux, France.
“Acoustics are another important aspect, and it’s related to the fuel block performance, because if it’s not properly done, then it will have to be compensated somehow with other solutions which will affect the cost, reliability, all sorts of things,” Cottenceau says.